Hey, check this out:
and
This fellow came up with a way to make jacketed .40 S&W bullets out of 9mm cases. He selects cases from the same manufacturer, and then weighs them so the weights are all the same. Then, he casts lead bullets (I already have the mold!), and plops them in the cases, and runs them through a single forming tool. His results look funny, but shoot great!
http://www.backwoodshome.com/forum/vb/showthread.php?t=3118
There's a video on the web of a different guy doing the same thing:
http://s636.photobucket.com/albums/uu87/BTSniper/?action=view¤t=P1020390.flv
That's mentioned here:
http://castboolits.gunloads.com/showthread.php?t=70121
I have tons of 9mm brass!!! The swaging die costs a mere $120. Gotta come up with a press to handle it. What do you think?
BTW, I used to swear at the 9mm that fit inside the .40 S&W's when I am sorting range brass. Now, it makes sense to me. The 9mm's are perfect as bullet jackets for the 40's.
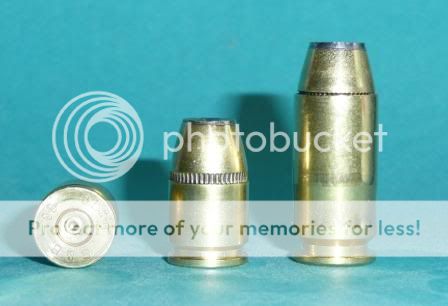
and

This fellow came up with a way to make jacketed .40 S&W bullets out of 9mm cases. He selects cases from the same manufacturer, and then weighs them so the weights are all the same. Then, he casts lead bullets (I already have the mold!), and plops them in the cases, and runs them through a single forming tool. His results look funny, but shoot great!
http://www.backwoodshome.com/forum/vb/showthread.php?t=3118
There's a video on the web of a different guy doing the same thing:
http://s636.photobucket.com/albums/uu87/BTSniper/?action=view¤t=P1020390.flv
That's mentioned here:
http://castboolits.gunloads.com/showthread.php?t=70121
I have tons of 9mm brass!!! The swaging die costs a mere $120. Gotta come up with a press to handle it. What do you think?
BTW, I used to swear at the 9mm that fit inside the .40 S&W's when I am sorting range brass. Now, it makes sense to me. The 9mm's are perfect as bullet jackets for the 40's.
Last edited: