Ok, so Jasper's post, with his in-transit HP casting mold got me to thinking:
How about my own plated bullets. I'd love to be able to make plated Hollow Point (HP) bullets. Not that the ones from Berry's aren't cheap, and don't work well. I'd just like to be able to do this all at home. So, I am starting this thread to peruse the working of doing such plating.
Links:
http://www.finishing.com/294/14.shtml
http://74.125.93.132/search?q=cache...ets&cd=2&hl=en&ct=clnk&gl=us&client=firefox-a
http://forums.handloads.com/forum_posts.asp?TID=22347&PN=1
http://www.finishing.com/0200-0399/323.shtml
http://forum.caswellplating.com/electroplating-questions/4473-copper-plating-lead-bullets.html
http://www.calguns.net/calgunforum/showthread.php?t=192471
http://www.finishing.com/0000-0199/064.shtml
http://dwb4.unl.edu/Chemistry/labs/LABS15.html
http://www.youtube.com/watch?v=-pjsLZ5EtXc
http://www.youtube.com/watch?v=rF1ls-v7puQ&feature=related
(there are tons of "related videos" for the viewing..)
How about my own plated bullets. I'd love to be able to make plated Hollow Point (HP) bullets. Not that the ones from Berry's aren't cheap, and don't work well. I'd just like to be able to do this all at home. So, I am starting this thread to peruse the working of doing such plating.
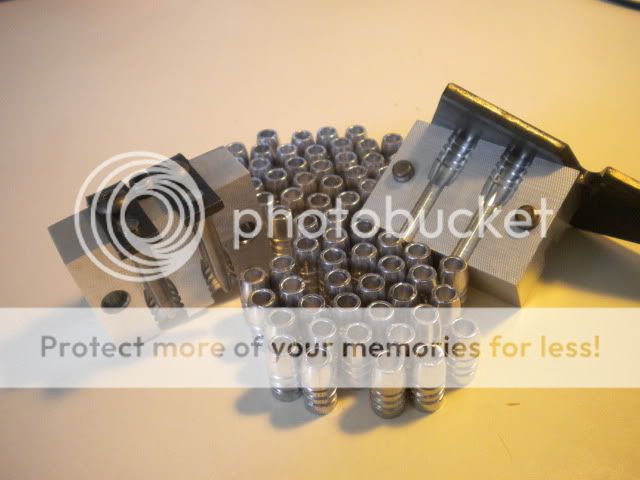
Links:
http://www.finishing.com/294/14.shtml
http://74.125.93.132/search?q=cache...ets&cd=2&hl=en&ct=clnk&gl=us&client=firefox-a
http://forums.handloads.com/forum_posts.asp?TID=22347&PN=1
http://www.finishing.com/0200-0399/323.shtml
http://forum.caswellplating.com/electroplating-questions/4473-copper-plating-lead-bullets.html
http://www.calguns.net/calgunforum/showthread.php?t=192471
http://www.finishing.com/0000-0199/064.shtml
http://dwb4.unl.edu/Chemistry/labs/LABS15.html
http://www.youtube.com/watch?v=-pjsLZ5EtXc
http://www.youtube.com/watch?v=rF1ls-v7puQ&feature=related
(there are tons of "related videos" for the viewing..)